
Services.
Welding Inspection :
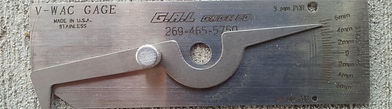
Weld Tech Australia : Offers a variety of inspection services to it clients. We are one of the few organisations that can provide senior welding inspectors and coating inspectors. Our diverse team has the right mix of relevant qualifications, knowledge and experience. The team is carefully selected and trained and they all have the necessary underpinning knowledge (ie. a trade background) to ensure the service we provide are practical and value add to your project. So whether you are an asset owner, engineer, design, procure and construct contractor or a fabrication company. Weld Tech Australia can assist you meet your projects quality objectives by undertaking inspection activities on your behalf. We service the Pressure Equipment and Structural manufacturing sectors for the Mining, Power Generation, Petroleum, Chemical, Defence industries.
We can offer you services in:
-
Pre inspection meetings.
-
Pre fabrication Vendor document reviews.
-
Fabrication and Welding Inspection.
-
Dimensional Inspection.
-
Visual welding Inspection.
-
Final Inspection.
-
Coating Inspection.
-
MDR reviews.
-
Pre fabrication Vendor document reviews.
-
Internal Audits on QMS Systems.
So what is welding inspection and why is it important?
Welding inspection can mean different things to different people. There are Australian standards and controlling documents on qualifications of inspection personnel. These standards and documents list functions from contract / drawing review to preparation for dispatch as tasks of a welding inspector.
So welding inspection is more than visually examining a weld to ensure it conforms to the standard with regard to weld discontinuities and AS1554.1-2011 states that ‘Prior to and during welding, the welding inspector shall inspect the set-up of work and ensure that – welds are in accordance with drawings, welding is carried out on specified equipment, correct procedures are maintained and work is performed in accordance with the standard.
Typically Welding Inspection is controlled by an Inspection and Test Plan (ITP). Welding Inspection can include drawing review, material control, material cutting and shaping, process and operator qualification, material welding, production process control, dimensional control, NDT coordination, PWHT verification through to coating, dispatch,bolting procedures and preparation of manufacturing documentation (MDR’s).
A welding inspector operates as the judicial representative of an organization, whether it be a purchaser, manufacturer, insurance company or regulatory authority like government.
The inspector has the role of monitoring progress which includes examining welds and ensuring all aspects meet the acceptance criteria which is often a mix of AS/NZ/ASME standards and purchasers specifications.
The inspector has to interpret the contract document, codes and specifications and apply the intent of the document to construction. Highest quality is the goal, but production cost, time lines are tempering factors. Delays must be avoided at all costs.
A welding Inspector is someone who should have:
-
Excellent communications skills.
-
Good technical knowledge.
-
Professional attitude.
-
Sense of Humour
They must be able to understand:
-
The when, how and why of welding inspection?
-
A welding inspector is your eyes and ears on the work front.
Why use Inspection?
This suggests while no one is watching what is coming out at the end of the production line, there is no accountability and operators produce what they think is acceptable, and after all if no issues are detected there is no problem, right, well maybe, maybe no one is looking.
All it takes is a few components to get rejected due to non conformance and the bar is suddenly raised and they understand that if it is not good enough it needs to be repaired. For some fabrication/welding workers, if they are not monitored, they think they can slap it together and get away with it!
Of course all of this can be avoided or reduced if you are successful in developing a workplace culture that promotes excellence and pride in workmanship.
So what can we offer?
Full time welding quality control or scheduled random site visits to evaluate weld quality at various stages of construction.
Our inspection service to you will consist of confirming that all welders are using qualified WPSs and hold valid qualifications, insuring the correct weld consumables are used, that welding consumables are stored as per manufacturers recommendations, that there is no damage to components through handling and transport, proper torque values at bolted connections are met, weld details as stated in drawings are duplicated in the field, completed welds are the required size and length, and that welds conform to the specific acceptance criteria.
Additionally we can verify dimensions of components to ensure that components are built as specified.
So whether it is Visual inspection or more detailed review, or Site representative and surveillance, Let Weld Tech Australia help you achieve your projects quality needs.
Welding Supervision:

Supervision : is a critical part of process control, without it an organisation usually is inefficient and its output lacks consistency.
The supervisor plays an important part as QA/QC.
Often manufacturing organization get it wrong with the application of Quality Assurance / and Quality Control. The basis of achieving quality is ‘control the process and the outcome will take care of its self.
Welding is a complex production process. Like any production process, if left uncontrolled the results can be disastrous. Using sound welding management principles you should complete your research and development on the most cost effective way to weld the component, set the appropriate parameters for the conditions, test the weld to ensure it conforms to the acceptance criteria, then and only when your welding process has been refined and verified do you release it into production, ensuring all welders/ operators follow the set procedure.
This is how to effectively control the welding process If operators determine their own settings production control is lost, causing issues such as undersize or oversize welds, lack of fusion, reduced productivity, increased repair rates etc.
Once you have control of the production process, the next step is to ensure your welding operators are adequately trained to carry out the task and understand what is required.
Good operators inspect their own work, but welding operators are just one part in a long list of variables (and people) involved in ensuring quality welds. If an organization is to keep its reputation and bottom line intact, control of the process and communication of the welding parameters, combined with appropriate education are paramount factors in achieving this.
Often manufacturers blame welders for repairs and rework, often this blame is incorrectly allocated, at the end of the day welding operators are like production line workers, smart ones, but none the less they are a part of the production line. I doubt Henry Ford would have had his line workers determine how to best do things, if you are smart you include them in the process and value their input into the process but ultimately the production process should be controlled by management. So when welds are under or over size ‘do not blame the tools’ (the welding operator) consider effective process control.
So rather than waiting to the end of the welding production line and the applying NDT and hope that it passes, why not let Weld Tech Australia can, assist you in implementing welding supervision while controlling the process giving you confidence and assurance you are meeting your quality targets.
Training Service.
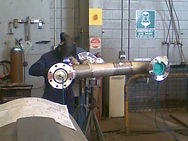
Weld Tech Australia not only has the practical experience to fulfil this need, we have extensive experience in education and understand the elements that make up a successful welding training program. Whether it is basic GMAW welding or advanced welding inspection, Weld Tech Australia can provide the welding training your organisation needs.The use of exotic materials is becoming more prevalent in all industries and the welding of these exotics can be challenging. Weld Tech Australia understands what it takes to weld exotic materials and has delivered welding training programs to its clients from Engineer level to the shop floor. We transfer the required knowledge where it is needed most.Weld Tech Australia"s Principal has National and international recognised supervision and inspection qualifications, ensuring a successful combination of technical knowledge and how to deliver it.These attributes compliment the twenty plus years experience in the fabrication and welding of pressure equipment and steel structures to Australian/New Zealand and American standards, using a variety of materials including exotics such as Chrome/ Super-Austenitic and Super-Duplex stainless steel.If you are looking for further information from us for welding training, please get in contact with us here.
Development Service.

Weld Tech Australia has extensive experience across a range of projects and industry sectors allows it to provide the right documents for your QA needs, from writing contract technical specifications for vendors to set project quality parameters, to the development of ITP’s to ensure all critical areas are identified, to welding procedures and welder qualifications, to the compilation of complete MDRs. Weld Tech Australia understands the importance of keeping welding management uncomplicated, and we use our practical experience to ensure key areas of the process are controlled but documentation is minimised. We use our staffs welding experience to develop practical welding procedures that are specifically designed to increase productivity, reduce rework and fulfil the relevant standard and specification requirements. Weld Tech Australia has a suite of welding procedures available to minimise cost and delays to projects. We can assist qualify your welders to the relevant standard and through their knowledge of standards, minimise cost associated with WQT.Weld Tech Australias extensive understanding of welding and welding procedures can refine your processes to achieve optimisation, reduce defects and reduce waste. Our staffs wide-ranging practical welding and supervision experience can be used to improve your workforces knowledge and skill. Welding Procedures are essential to ensuring your job is done on time, on budget and without mistakes.If you would like to get in contact with us about this service then please contact us here.